Knitted fabrics are known to have existed even before 256 A.D., evidenced by samples found in Syria and Egypt. This art of producing fabrics was introduced to Europe by the Arabs. |
|
|
Fig.1: Hand knitting with simple pin |
|
|
The first knitting machine was invented in 1589 - incidentally 200 years prior to French revolution - by Rev. William Lee of Nottingham. In hand knitting, yarn is looped around pin (s) in the manner shown in Fig. 1. |
The resultant fabric, a matrix of rows and columns of loops, is formed by creating a single element in each complete cycle of operation. Hence, if a fabric needs to have 100 loops in each row, then 100 cycles of operation would be needed to produce one row. Subsequently, loops of the row just completed would be transferred one after the other to another pin and in the process new elements are generated for the next row. The machine invented by W. Lee could however generate one complete row in each cycle of operation. |
|
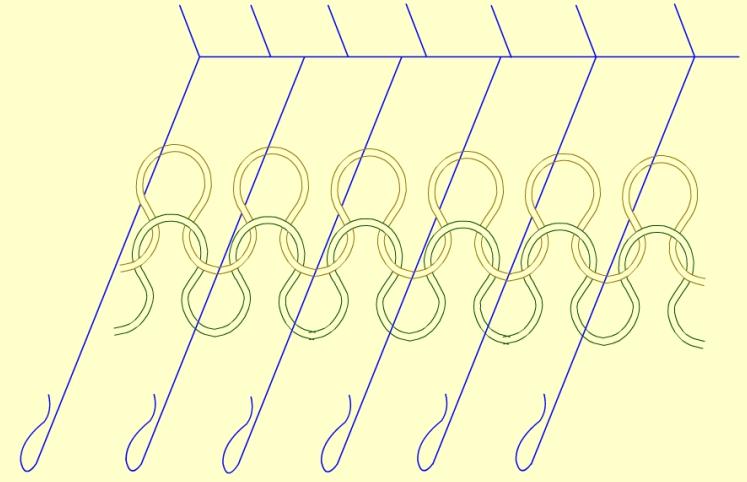 |
|
Fig.2: Mechanization of hand knitting
|
|
|
As shown in Fig 2, such machine has needles and each needle supports a column of the matrix, referred to in the foregoing. In each cycle of operation, all needles execute similar motion and produce a loop each. It is no wonder then that this method of production is immensely more productive than hand knitting. Such a qualitative change in method of production upsets the existing system considerably and so the Rev. Lee was accordingly hounded out of his native land. It took nearly 2 more centuries before any further development in mechanization of knitting process could take place. The real surge in development of this technology is intimately linked with commercial availability of man-made filament yarns. Thus, the period subsequent to the Second World War has witnessed tremendous growth, such that currently internationa1 production of knitted fabrics matches the weaving method of fabric production. |
1.1 Basic concepts : |
The process of knitting, as practiced commercially, can be broadly classified into the following groups. |
|
There are, in principle, two broad classes of knitting processes namely WEFT KNITTING (Fig. 3) and WARP KNITTING (Fig. 4). |
|
Fig.3: Principle of weft knitting |
|
|
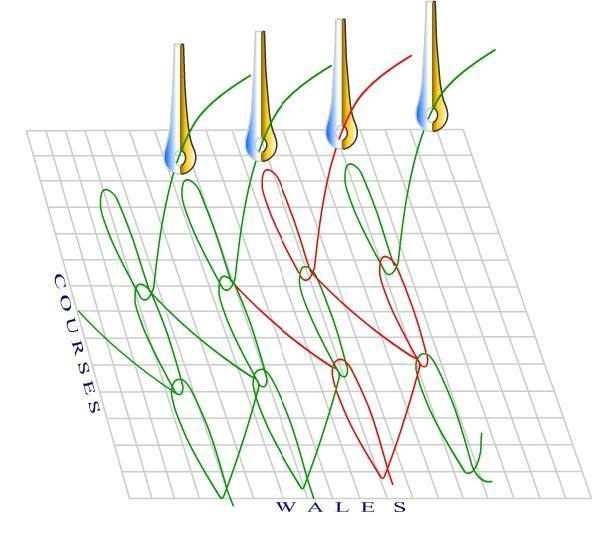 |
|
Fig.4: Principle of warp knitting
|
|
|
In WEFT KNITTING, the general direction of path of yarn is across the length of fabric. This is analogous to a pick of weft in weaving process. (Link to Video Clip 1) (Link to Video Clip 2) |
In WARP KNITTING the general direction of path of yarn is along the length of the fabric, similar to that of warp in weaving. (Link to Video Clip1) (Link to Video Clip2) |
Moreover, weft-knitting can be carried out from one single spool, analogous to a package of weft .
(Link to Video Clip) |
For warp knitting, on the other hand, one needs a warp beam. |
A WALE is a column of loops intermeshed with each other along the length direction of a knitted fabric. In Figs. 3 and 4, four wales or wale-lines are shown. The distance between centers of neighboring wale lines is known as WALE-SPACING (w). The number of wales in unit width of fabric is designated as W. |
A COURSE is a row of loops produced by adjacent needles during the one knitting cycle. In Figs. 3 and 4, three courses are shown. The distance between the courses of two successive needle loops of the same wale line is known as COURSE-SPACING (c). The number of courses in unit length of fabric is designated as C. |
The product of the number of wales per unit width and courses per unit length of fabric equals the number of loops per unit area of the fabric. This is designated as STITCH DENSITY (S). Stitch density happens to be a more accurate measurement than linear measurement of courses and wales because tension acting in one direction of the fabric may produce low reading in, for example, the courses/unit length and high reading for the wales/unit width. When multiplied together, this effect cancels out to a degree. |
The production process of knitted fabrics can be represented by the following flow diagram. Both warp and weft knitting processes are evidently much simpler than the weaving process. |
|
The KNITTED FABRIC can be defined as a two dimensional continuum, produced by looping around (intralooping and interlooping) of individual yarns or sets of yarns. The building block of a knitted fabric is the LOOP. In a woven fabric, yarns are held in place owing to inter yarn friction. In a knitted fabric the looping of yarns results in positive binding. |
LOOPS are stitches hanging on to one another (Fig. 5) and held in shape on the upper and lower interlacing zones by other loops. The last row of knitted loops in a fabric is only bound at the lower zones and can be referred to as half-loop. |
|
|
Fig.5: A Weft knitted loop and its elements |
|
|
If the feet (c) of a loop lie above the binding points at the base, and the arms (b) lie below (Fig. 6), then the loop is being viewed from the TECHNICAL BACK side. If, on the other hand, the feet (c) are below the binding points and the legs (b) are above, then the TECHNICAL FRONT of the loop (Fig. 7) is being viewed. |
|
Fig.6: The technical backside of a loop |
|
|
|
Fig.7: The technical front side of a loop |
|
|
Incidentally, the crown (a) is known as needle loop. The two elements “c” if joined together on the same side of the loop would result in a mirror image of element (a). This so joined element is also known as sinker loop. |
|